Machining Research
The metal cutting or machining is a process of geometrically defined removal of material. Localized shear of a metal being cut leads to strain, strain rate and temperature far beyond the majority of other manufacturing processes. We work to explore, solve and innovate in all aspects of machining research.
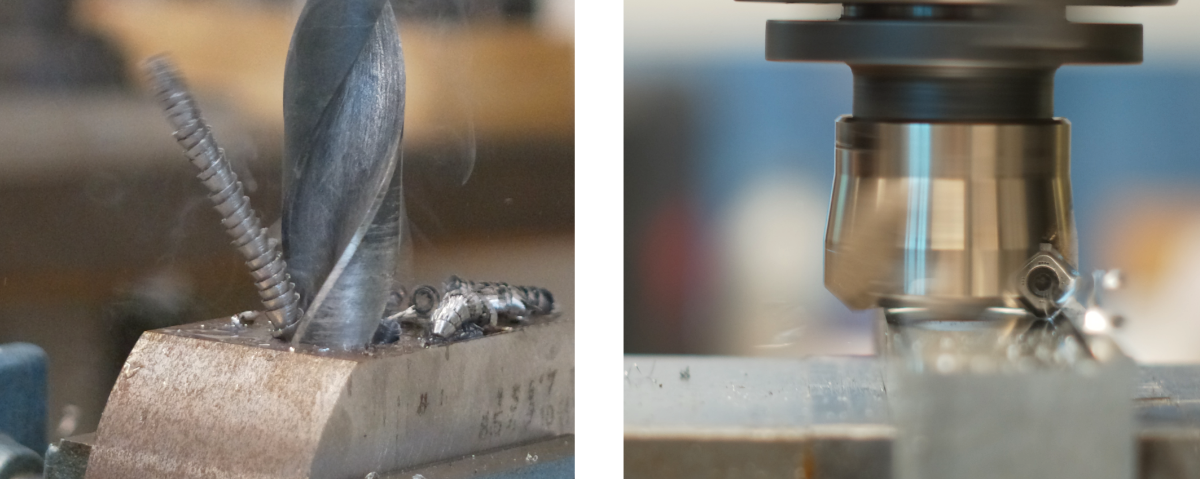
Machining performance
Machining, as a manufacturing process, is at the intersection of mechanics, thermodynamics, materials science and tribology. Such complexity makes the machining performance highly unpredictable. Our research covers questions of process mechanics (e.g. chip formation, forces, vibrations), thermal phenomena, tribology and tribo-chemistry. We study machining performance for metallic materials, fiber reinforced polymers and metal matrix composites.
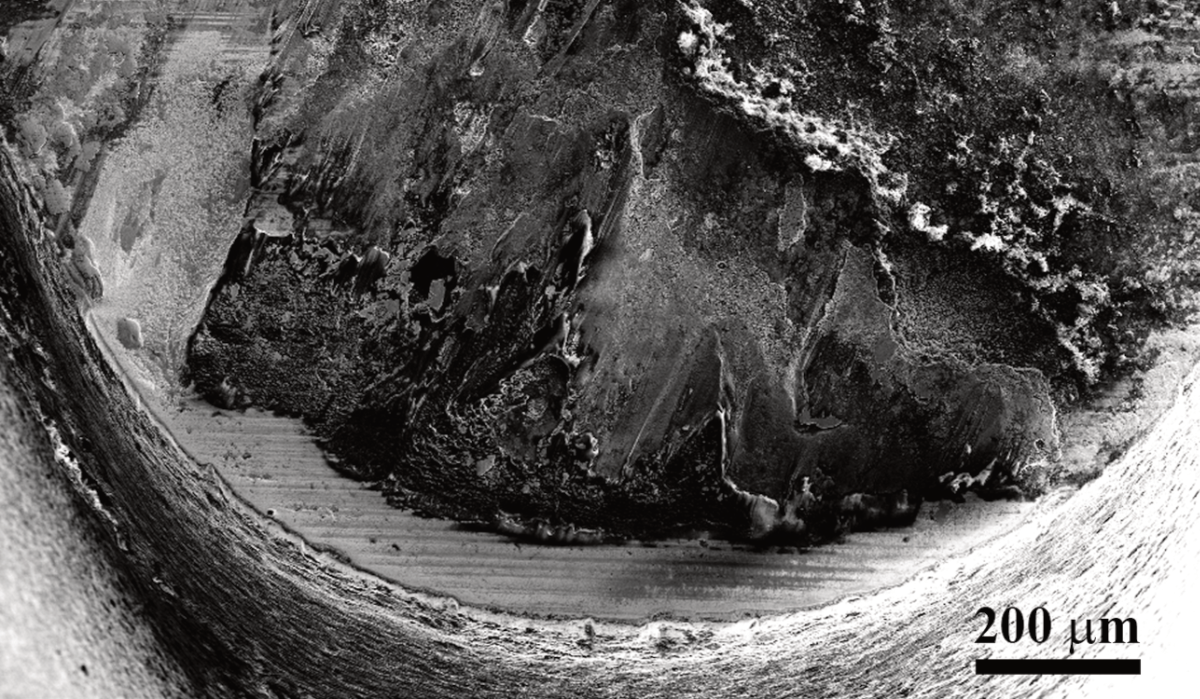
Tool wear and degradation
In machining, the tool experiences extreme temperature, sliding speed and pressure while staying in intimate contact with the being cut material. We work with analysis of individual wear mechanisms (abrasive, adhesive, oxidation, diffusional and chemical) and their interplay under multi-mechanism interaction. In-depth analysis relies on advanced material characterization and computational predictive modelling.
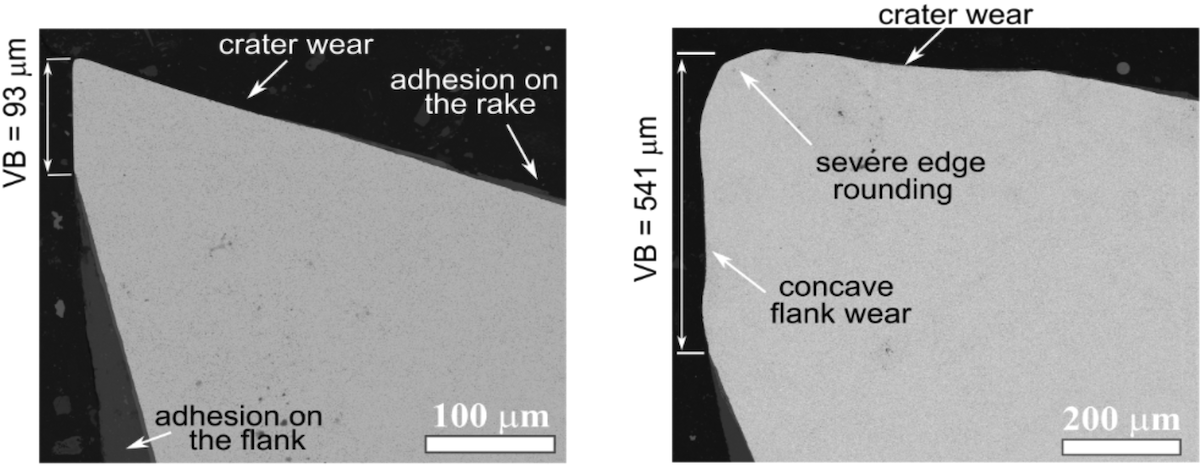
In recent years we have discovered that tool-workpiece-environment interaction may not lead to the tool wear. On the contrary some of the reaction products are refractory metal nitrides (e.g. (Ti,Cr,Nb)N [Bushlya, 2021]), borides (e.g. (Ti,V)B2 [Lindvall, 2020]), carbides (e.g. NbC [Olsson, 2020]), oxides (e.g. FeAl2O4, MgAl2O4 [Bjerke, 2021])). These products act as a Tool Protection Layer (TPL).
- Lindvall, 2020 - Performance and wear mechanisms of PCD and pcBN cutting tools during machining titanium alloy Ti6Al4V
- Olsson, 2020 - Study of wear mechanisms of cemented carbide tools during machining of single-phase niobium
- Bushlya, 2021 - Tool wear mechanisms of PcBN in machining Inconel 718: Analysis across multiple length scale
- Bjerke, 2021 - Onset of the degradation of CVD α-Al2O3 coating during turning of Ca-treated steels
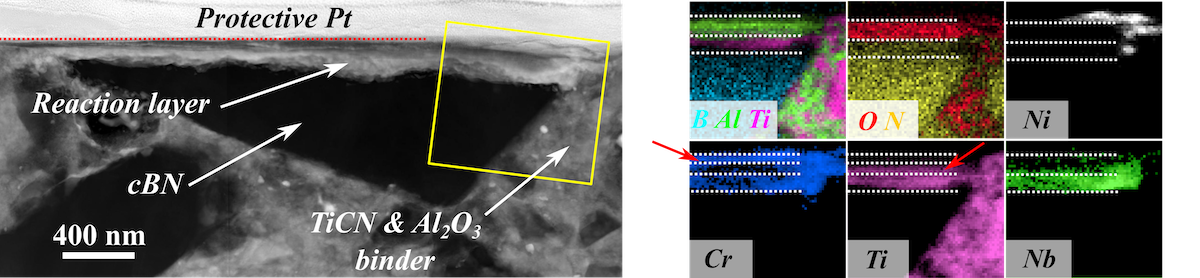
Machinability of materials
Machinability of materials is another topic of our research. It covers the influence of composition, heat treatment, inclusions, trace elements and micro-alloying of metallic materials on their machinability.
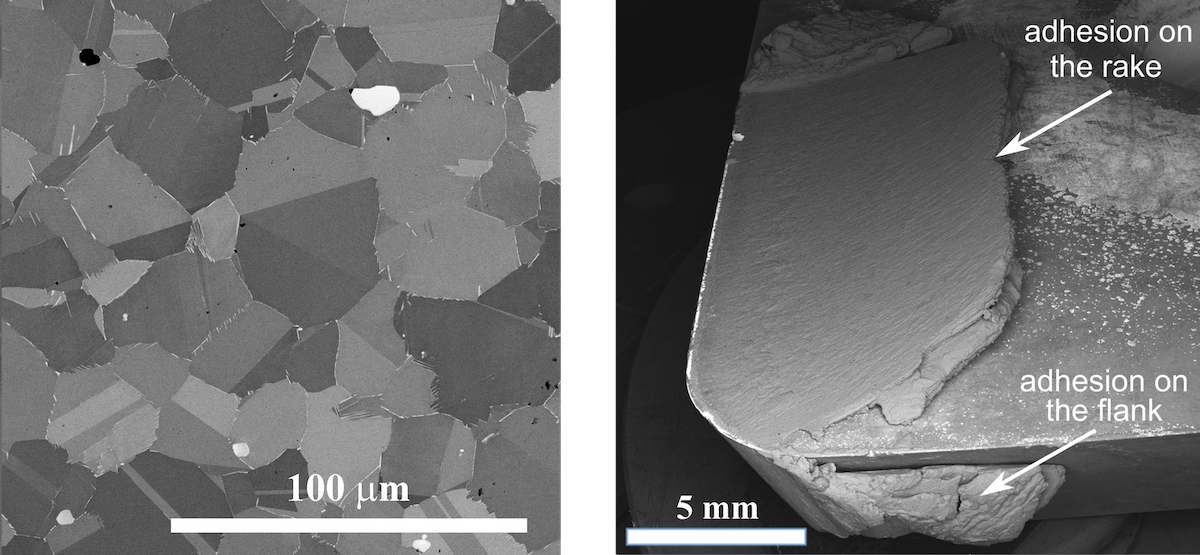
Based on the findings related to Tool Protection Layer, we have developed a concept of increased machinability of metallic materials via controlled micro-alloying which relies on controlled and continuous in-situ formation of a protective layer on the tool surfaces that is built-up of refractory reaction phases.
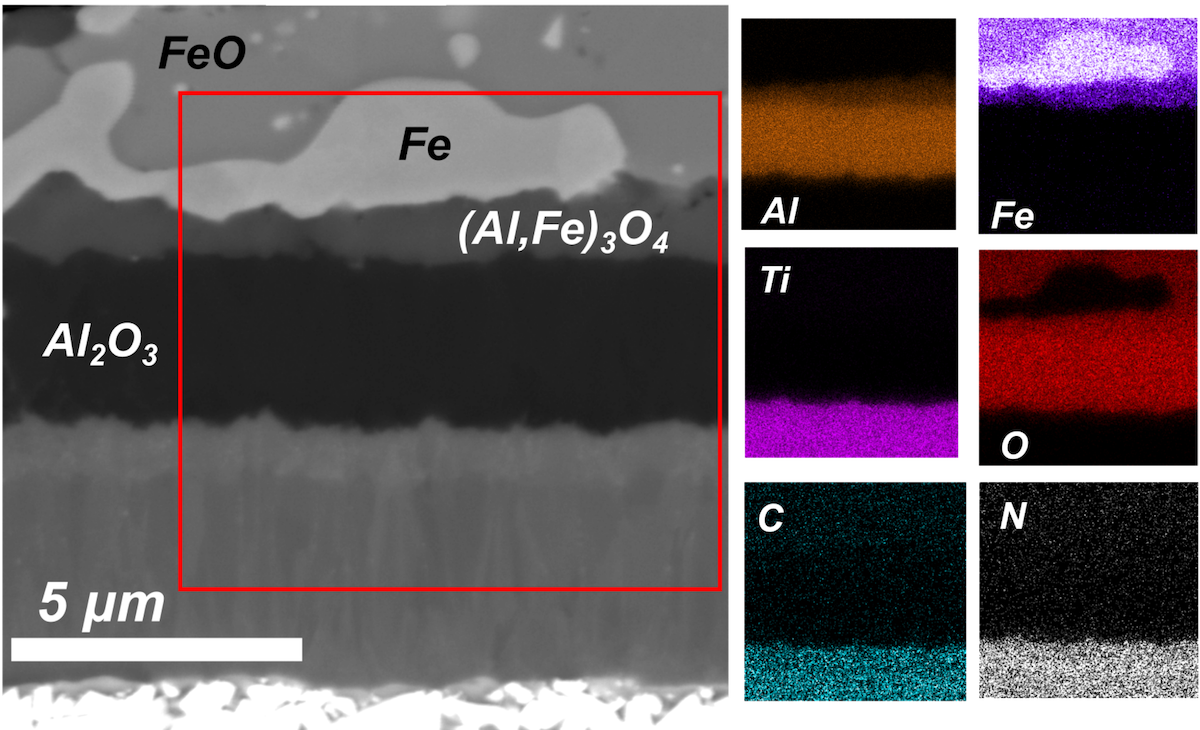
Tooling and tool materials
We work with the design and sintering of superhard polycrystalline cubic boron nitride (PcBN) and polycrystalline diamond (PCD) advanced materials for tooling applications. Our latest developments are developed for high performance machining of Ni and Ti superalloys
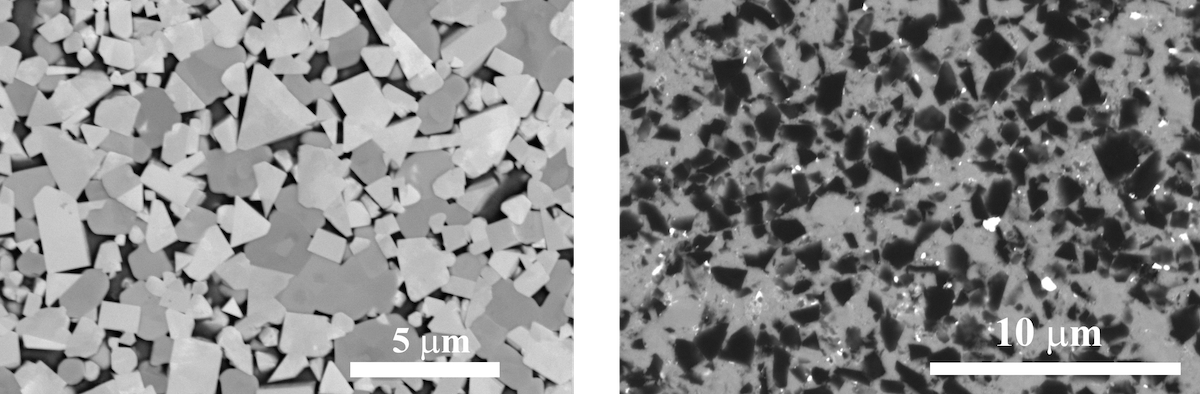
Another area is coating research, in particular design of physical vapor deposition (PVD) coatings based on their response to wear mechanisms.
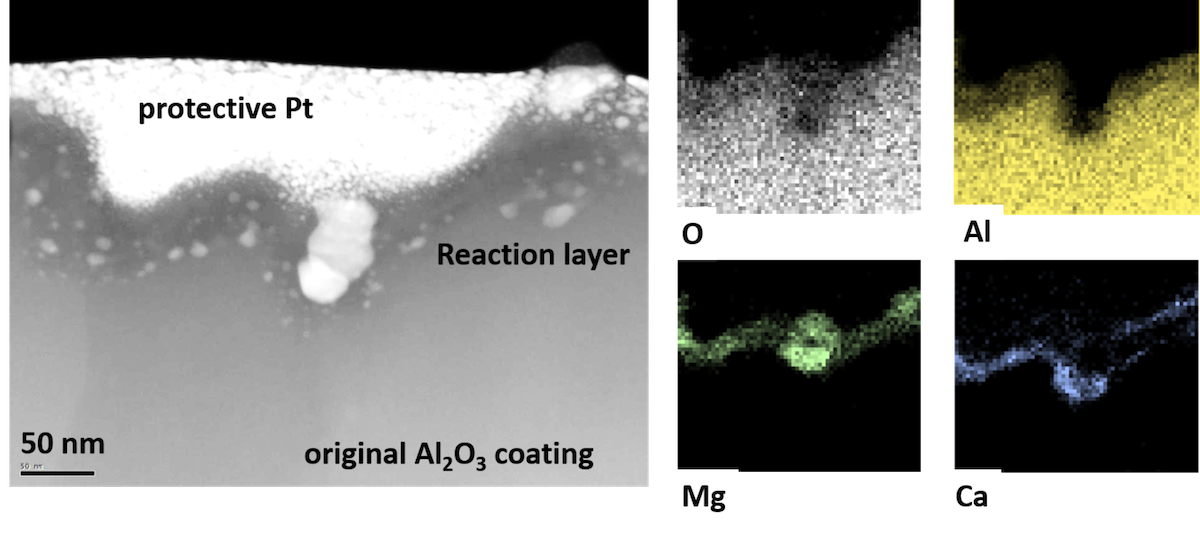
Modelling and Simulation of Machining
Drive for machining efficiency relies on predictability of process behavior. We work with modelling and simulation of mechanical and thermal phenomena in machining. The questions of chip formation, cutting forces, tool stresses, and surface integrity (sub-surface deformation and residual stresses) are routinely investigated in order to optimize the machining process, improve cutting tool design, match tool and workpiece materials, etc.
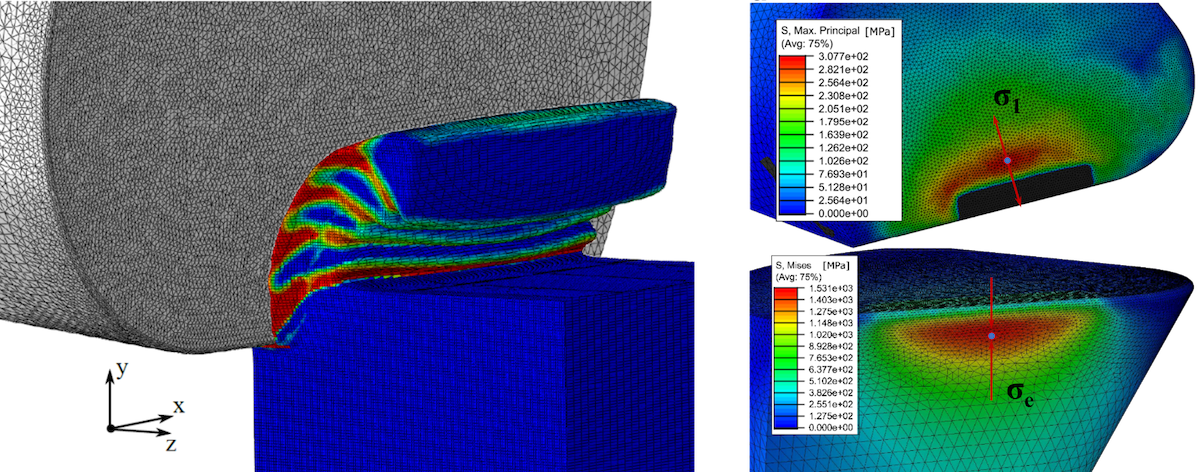
We have also developed a modelling framework to describe the chemical and diffusional interaction of the cutting process. These models have been used to characterize the wear of cutting tools, and to find materials and condition when the interaction products reduce the wear rate and protect the cutting tools.
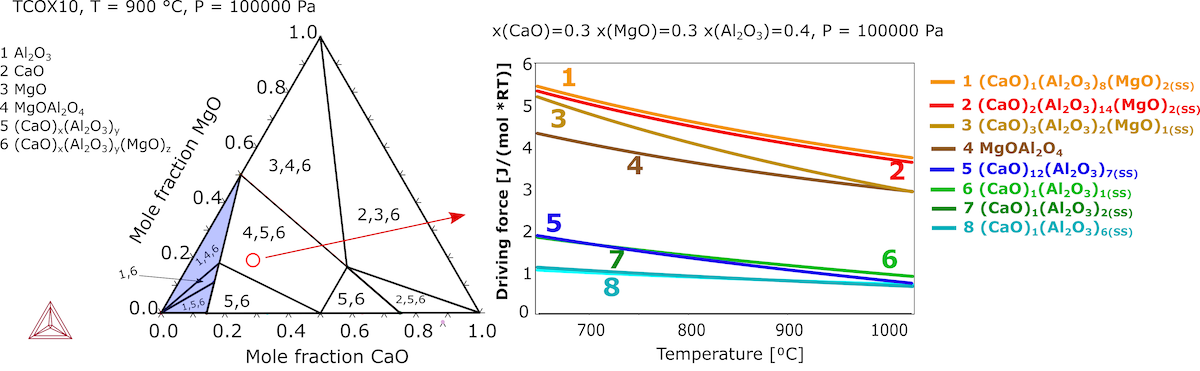
Surface integrity
Characterization of surface integrity may entail inspection for surface defects (cracks, porosity, build-up edges), measurement of sub-surface deformation and stresses, or analysis of phase transformations, whichever dictates performance or failure via fatigue, corrosion or other mechanisms.
Surface integrity refers to the state of machined surface and sub-surface layer in terms of composition, microstructural and mechanical properties which jointly define product performance.
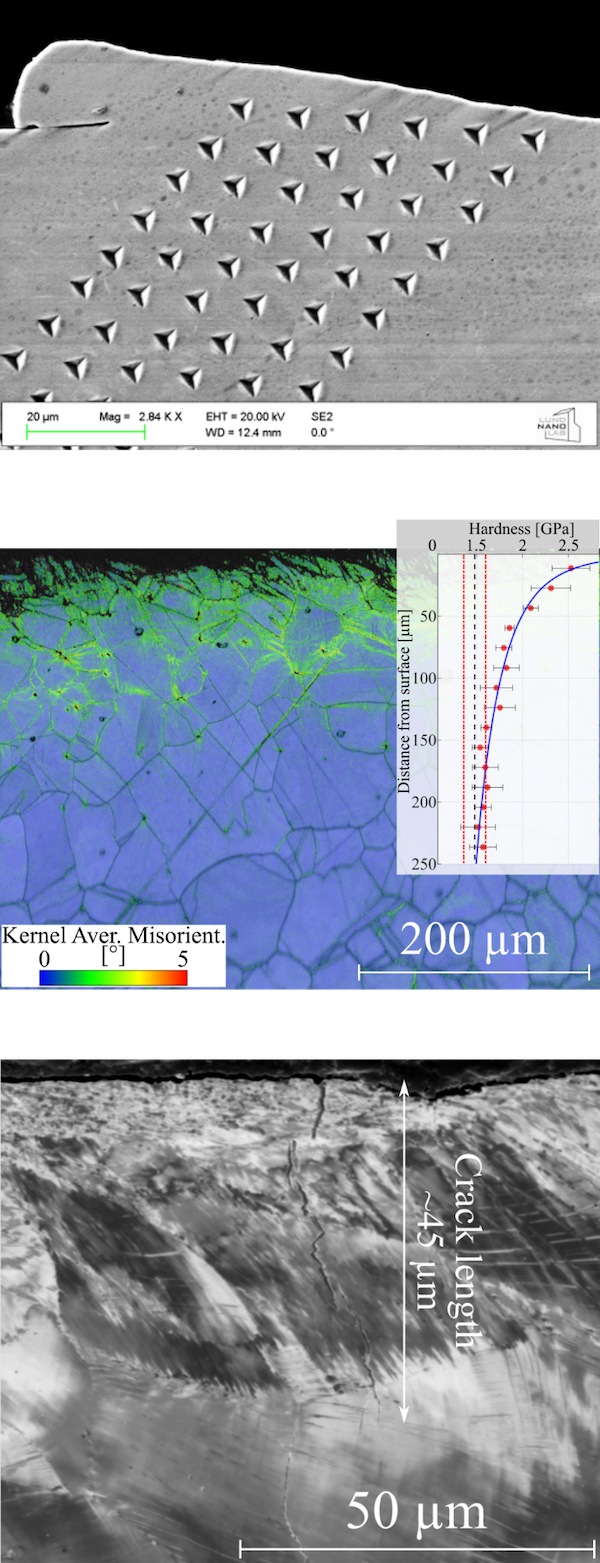
Volodymyr Bushlya, volodymyr.bushlya@iprod.lth.se, 2023